Contemporary plastic manufacturers serve a variety of industries, from B2B manufacturing to supplying precision parts and components for critical and safety-oriented sectors. Find a partner who offers advanced manufacturing capabilities that are suited to your project’s unique requirements.
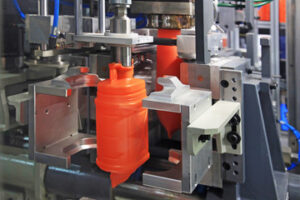
Look for a manufacturer that offers comprehensive product development, from prototyping to production runs. The right manufacturer can also provide rapid turnaround time and automated quality control. Read on Plastic Manufacturers In Miami for more details.
Plastic is a versatile and highly effective material that can be molded into many different shapes, sizes and forms. To produce the best-quality plastic products, manufacturers need to be skilled in the latest manufacturing techniques and have a deep understanding of the unique properties and applications of each type of plastic. To ensure they are able to meet industry standards, they must also stay up-to-date on the latest regulatory compliance and certification requirements.
To remain competitive in the rapidly evolving manufacturing landscape, plastics manufacturers must also be able to leverage new technologies and methodologies that increase productivity, reduce costs and improve efficiencies. These advancements include automation, artificial intelligence (AI) and real-time data analytics. To fully harness these capabilities, they need employees with digital proficiency and a strong commitment to continuous learning and innovation.
Critical industries rely on the integrity and performance of plastic products. Partnering with a plastic manufacturer without the relevant industry expertise can lead to design flaws, suboptimal materials selection and substandard manufacturing processes, all of which can negatively impact product quality and reliability. To avoid these risks, choose a plastic manufacturer that has extensive experience working with the specific industry in which you work and can provide proactive support throughout the design process, including engineering assistance, material selection guidance, and flexibility to accommodate your changing project needs.
Plastics are made from a variety of raw materials, which are then combined using additives like heat stabilizers, lubricants, fillers and plasticizers to achieve the desired physical properties for each application. These additives can have a significant impact on the color, strength, density, working temperature range, corrosion and heat resistance of a finished plastic.
Due to environmental concerns and increasing consumer demand for sustainable products, plastic manufacturers are exploring ways to promote sustainability and reduce waste. They are implementing recycling programs, sourcing recycled or biodegradable materials and committing to a circular economy model in which waste is reused to produce new products. In addition, they are collaborating with suppliers and logistics providers to reduce the environmental impacts of transportation. These initiatives are helping to reduce reliance on fossil fuels and minimize carbon emissions.
State-of-the-Art Manufacturing Capabilities
A contemporary plastic manufacturer needs to be capable of handling a wide variety of custom project requirements. Look for a manufacturer that is equipped with high-speed production machines, the ability to work with a variety of engineering-grade materials, and an experienced design team. This way, you can be confident that your plastic product will be developed and manufactured to the highest standards.
Injection molding is one of the most common manufacturing processes for specialized plastics. This process involves heating and combining plastics to form the desired shape, which is then cooled and inserted into a mold to keep the product intact. Injection molding is highly versatile and can be used to create everything from small medical devices to large automotive components.
Another popular plastic manufacturing method is thermoforming, which combines heat and vacuum to transform plastic sheet materials into complex shapes. This allows for a greater level of customization and often reduces production costs, as it may not require tooling or metal fabrication. Thermoforming is particularly well-suited for creating packaging, reusable totes and trays, automotive appliques, and clamshells.
A quality plastic manufacturer should also have a robust research and development (R&D) program. This will allow them to develop and test prototypes of new products to ensure that they meet industry specifications, comply with regulations, and provide a competitive advantage for their clients. RMC Plastics, for example, uses its extensive prototyping capabilities to help customers overcome technical challenges and enhance their product’s functionality.
In addition, a quality plastic manufacturer should be able to support their clients’ sustainability initiatives by using recycled materials in their production processes. This helps to reduce waste and lower energy consumption, which is especially important for industries such as defense and aerospace that rely on high-quality, precision parts and components that must be durable and reliable. Vantage Plastics’ Edge Materials Management division is a perfect example of this, as it efficiently collects, processes, and recycles various types of post-industrial and post-consumer scrap plastic to create a closed-loop supply chain that supports sustainable manufacturing.
Strong Sustainability Focus
The plastics industry is making progress in addressing the challenges posed by mismanaged waste. However, achieving sustainable plastic manufacturing requires collaboration between manufacturers, consumers, regulators, and stakeholders throughout the value chain. A strong commitment to sustainability can be demonstrated through a range of practices, including utilizing sustainable materials, adopting closed-loop systems, and implementing energy-efficient production processes.
A comprehensive sustainability strategy also involves minimizing environmental impacts by using renewable and recycled materials, ensuring minimal pollution and emissions, reducing water usage, and promoting worker safety. Additionally, companies should minimize the use of non-renewable fossil fuels and promote greener alternatives. Finally, a successful plastic manufacturer should be able to provide full product development services, from prototyping to high-volume production.
Whether you’re producing products for the aerospace, medical, or automotive industries, it’s important to ensure your plastic manufacturer is fully compliant with all relevant regulations and standards. Look for a manufacturer that has extensive experience working with the specific requirements of these industries, and that can offer a variety of industry-leading technologies, materials, and manufacturing processes.
While implementing new technologies, materials, and production processes to improve sustainability can be costly, the investment can pay off in reduced energy consumption, waste, and operating costs. In addition, a focus on sustainability can help build brand loyalty among eco-conscious consumers.
One of the most important aspects of a plastics manufacturer’s sustainability strategy is utilizing sustainable raw materials, such as bio-based plastics made from renewable resources and recycled plastics. These materials are less toxic than synthetic options, and they help reduce the industry’s dependence on fossil fuels. In addition, plastic manufacturers can implement closed-loop systems that allow them to recycle unused raw materials and cut down on the amount of waste they generate.
Finally, a plastics manufacturer should employ regular safety audits and inspections to identify potential risks and areas for improvement. These efforts can be further supported by the use of automation technology, which allows workers to perform repetitive tasks safely and accurately while reducing their exposure to hazardous conditions. In addition, a strong commitment to sustainability can be communicated through transparency initiatives that involve publishing detailed breakdowns of materials used, energy usage, and more.
Effective Collaboration
Plastics are a massive global issue, but they’re also a huge opportunity to address pollution and climate change. Many companies and governments are taking bold steps to create new solutions that will keep plastic waste out of the environment, but there’s a lot more that needs to be done. One of the most important things is a coordinated effort to ensure that plastic recycling and reuse efforts are as effective as possible.
In the past, industry/academic collaborations have been relatively ineffective, largely due to issues related to intellectual property (IP). The problem of IP ownership has long been a barrier to sharing research data and discoveries between universities and companies, but there are some promising developments that may help improve these partnerships.
The most effective models of industry/academic collaborations have two primary elements: transparency and communication. Transparency refers to a willingness to share information and openly discuss problems and potential solutions with partners. It also relates to the ability to work together, despite differences of opinion or background. Effective communication refers to the ability to share and understand complex technical data and concepts.
Another key aspect of effective collaboration is the ability to identify and connect with new resources. This is particularly true when it comes to identifying sustainable and alternative feedstocks. It’s important for manufacturers to be able to access and evaluate the availability and efficiency of alternative feedstocks before they can begin production.
This is an increasingly urgent and challenging issue, and the best way to make progress is through collaborative action. Many organizations are now focused on using recycled plastics in their products, but it’s not easy to do so without the right tools and support. The need for better measurement and metrics is driving a growing number of initiatives to develop scalable and practical tools that can help businesses move beyond linear models of business and adopt more circular approaches.